Introduction to Investment Casting Technology
Investment casting process refers to the process of making a model with wax and wrapping it with a layer of refractory materials such as clay. Heating causes the wax to melt and flow out, resulting in an empty shell formed by the refractory material. The metal is then melted and poured into the empty shell. After the metal cools down, the refractory material is crushed to obtain the metal Mold. This process of processing metal is called precision casting, also known as investment casting or wax loss casting.
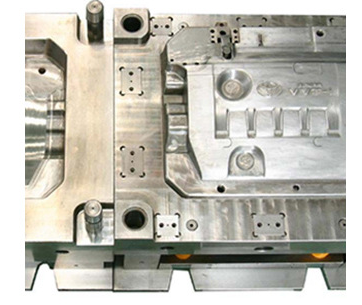
Advantages and disadvantages of investment casting process
Precision casting, also known as investment casting, has the following advantages compared to other casting methods and part forming methods:
1. Alloy materials are not limited: materials such as carbon steel, stainless steel, alloy steel, copper alloys, aluminum alloys, high-temperature alloys, titanium alloys, and precious metals can all be produced by precision casting. For alloy materials that are difficult to forge, weld, and cut, precision casting is particularly suitable for production.
2. High production flexibility and strong adaptability. It can be used for both large-scale production and small-scale or even single piece production.
In summary, precision casting has the advantages of small investment scale, large production capacity, low production costs, simplified complex product processes, and fast investment returns. Thus, it is in a favorable position in competition with other processes and production methods.
Key points of investment casting process:
1. Do not spray too much parting agent on the mold cavity.
2. Do not easily change the cycle parameters of the pressing melt (wax) mold after it is established.
3. The wax molds should be placed in a storage tray and isolated from each other to avoid damage. If necessary, fixtures, etc. can be used to avoid wax mold deformation.
4. Be careful not to damage the profile during the correction process.
Application scope of investment casting process:
Precision casting is applied to almost all industrial sectors, especially in sectors such as electronics, petroleum, chemicals, energy, transportation, light industry, textiles, pharmaceuticals, medical devices, pumps, and valves